3Dプリンタとは?仕組みや種類、特徴など解説
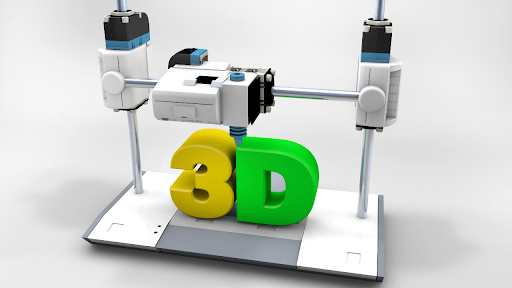
実用化されて以来急速に普及が進み、いまやものづくりに欠かせない存在として重要な加工方法の一つである3Dプリンタの技術。
3Dプリンターを自社でも導入したい、どのような使い方ができるのか詳しく知りたい、と考える企業も多いのではないでしょうか。
本記事では
・3Dプリンタとは?
・3Dプリンタの特徴
・3Dプリンタの造形方式の種類と特徴
などを解説します。
3Dプリンタについて知りたい方、これから3Dプリンタの導入を考えている方はぜひ最後までご覧ください。
3Dプリンタとは?
3Dプリンタは、3Dデータを元に立体物を作り出す機械です。
3Dのデータを薄くスライスして2次元形状を作り、その2次元形状を積み上げながら3Dデータと同じ形の立体モデルを作り上げていきます。
切ったり削ったりする除去加工や、素材の形を変形させる塑性加工、変形加工と異なり、材料を追加していく加工という意味で、アディティブマニュファクチャリング(additive manufacturing)とも呼ばれています。
通常のプリンタが紙にインクを使って平面的な絵や文字を印刷するのに対し、3Dプリンタはプラスチックや金属などの材料を少しずつ積み重ねることで、立体的な物体を作ります。
工程は、まず3Dデータをパソコンで作成し、それを3Dプリンタに送信します。
プリンタはこのデータを元に、材料を一層ずつ積み上げて形を作っていきます。
これにより、模型、部品、さらには日常品まで、様々なものを作ることが可能です。
例えば、おもちゃやスマホケース、さらには医療用の義肢まで作ることができます。
3Dプリンタは、今では加工方法の選択肢の一つとなり、ものづくりの現場に普及しています。
3Dプリンタの特徴
ここでは、3Dプリンタの特徴について解説します。
具体的には以下の通りです。
・3Dプリンタの仕組み
・3Dプリンタでできること
それぞれを詳しく見ていきましょう。
3Dプリンタの仕組み
3Dプリンタにはいくつかの種類がありますが、共通の原理があります。
それが積層して物体を作るという点です。
プラスチックや金属、セラミックなど、あらゆる素材で共通している原理です。
これまで物体を作る技術は
・塊を削る
・溶かして型に押し込む
の上記どちらかが主流でしたが、3Dプリンターは積み上げるという原理によって、新たな価値を提供し始めています。
3Dプリンタでできること
3Dプリンタは今や多くの分野で活用されており、製品の開発や製造においてより高い性能を発揮しています。
例えば、3Dプリンタは次のような場面や用途で活用されています。
◆試作品の作成
3Dプリンタによって試作品を作ることで、設計開発段階での形状確認や外観イメージの共有が可能です。
金型が必要な成形加工や、専用の切削工具を使う切削加工では、試作品のために型起こしや工具製作が必要となり、試作コストが大きくなりがちですが、3Dプリンタではそれらの準備が必要なく、低コストで試作品を作成して設計の評価を行うことができます。
◆型の作成
3Dプリンタでは、射出成形やプレス成形で必要となる金型の造形も可能です。
開発段階では、金型の設計に多くの時間を費やすことが多いです。
実際に成形してみて評価し、修正や改良を繰り返して量産体制に入ることになりますが、この修正や改良の手戻りに時間とコストがかかります。
こういった試作用の型を3Dプリンタで造形することで、低コストで試作を繰り返すことが可能になり、開発リードタイムを短縮することが可能になるのです。
◆機構確認
可動する構造のある製品や複数の部品を組み合わせる必要がある製品では、その機構が確実に機能するか、どこかに不具合が発生しないかを試作品によって確認しながら開発していきます。
もし、機構がうまく動かないようであれば、設計を見直さなければなりません。
そうなってしまった場合、試作品のために準備した型や工具が無駄になってしまうことがあります。
こういった機構の動きや部品の嵌合性を確認する用途でも、3Dプリンタは活躍します。
最終的には別の材料で制作することになる製品であっても、3Dプリンタでは機構を確認するために低コスト素材での試作が可能です。
◆製品の量産
3Dプリンタは、最終製品の製造ももちろん可能です。
小ロット生産品であれば、3Dプリンタで製造することで金型や治工具を製作する時間、コスト、手間を削減できます。
また、一定の需要があるのが生産終了品の復元製造です。
すでに生産が終了している部品は、その生産に使用していた型や治工具が使えなくなっていることもあります。
このような生産体制がすでにない製品でも、3Dプリンターによって復元することが可能です。
◆建築分野での活用
建築分野では、3Dプリンタで建築模型をつくり、物件の立体的な完成イメージを施工主に伝えることができます。
建築設計は3D-CADで行われることが多く、既に3Dモデルが存在するため、3Dプリンタによって建築模型を容易に造形することが可能です。
◆医療分野での活用
3Dプリンタでは、軟質素材で人の肌や組織に近いモデルの製造も可能です。
さらに短納期で製造可能なため、患者の症状に合わせたモデルを3Dプリンタで再現し、手術の前にシミュレーション用途で利用できることから、医療分野では3Dプリンタの持つ高い造形自由度と短い製造期間が注目されています。
また、カテーテルや内視鏡などの手技のためのトレーニングキット製造にも、3Dプリンターが活用されています。
3Dプリンタの造形方式の種類と特徴
ここでは、3Dプリンタの造形方式の種類とそれぞれの特徴について解説します。
造形方式については以下の通りです。
・熱溶解積層方式(FDM)
・光造形方式(SLA / DLP)
・インクジェット方式
・粉末床溶融結合方式(PBF=パウダーベッド方式)
・メタルデポジッション方式
それぞれを詳しく見ていきましょう。
熱溶解積層方式(FDM)
熱溶解積層方式(FDM)とは、3Dプリンタ世界シェアNo.1である米国Stratasys社が開発した方式です。
現在、3Dプリンタにおいて主流の方式でもあります。
熱で溶かした樹脂をノズルから押し出し、ソフトクリーム製造機のようなイメージで、一筆書きで1層1層積み重ねて造形していきます。
この画期的な方式はストラタシス創設者のスコットクランプがグルーガンを見て想起したという逸話が残っています。
材料の自由度が高く、装置の価格も比較的低価格なものが多いことから、広く普及しています。
熱収縮を考慮する必要があり、厳密な寸法精度を出す用途には向いていませんが、生産数量が少ない試作品や、試作段階における型の造形などに適しています。
光造形方式(SLA/DLP)
光造形方式(SLA/DLP)は最も古い3Dプリンターの方式です。
紫外線によって硬化する特性を持つ液体樹脂を材料として、紫外線照射によって一層ずつ硬化させ造形していきます。
光造形方式(SLA/DLP)は、造形に時間がかかるものの、大型の製品をつくることができるSLAと、比較的速い速度で造形できるものの大型の製品は苦手とするDLPのふたつの方式に分かれます。
エポキシ系樹脂やアクリル系樹脂などの透明樹脂による造形が可能ですが、強度の求められる用途には向いていませんが、なめらかな仕上がりにできるため、モックアップの製造に適しています。
インクジェット方式
インクジェット方式という通称もありますが、正式分類では材料噴射法と言います。
その名の通り、材料を噴射し、それに対し光を当てて1層1層積んでいきます。
構造が2Dプリンタでいうインクジェットプリンタに類似していることから、インクジェット方式と呼ばれています。
主材となる樹脂を噴射するマテリアルジェッティングと、粉末材料に対して結合剤を吹き付けるバインダージェッティングのふたつの工法があります。
マテリアルジェッティングは精細な造形や色分けをしながらの造形も可能です。
バインダージェッティングは骨格模型や砂型の製造など特殊な用途で使われることが多い工法です。
粉末床溶融結合方式(PBF=パウダーベッド方式)
パウダーベッド方式は、金属粉末を敷き詰めた床に光線を照射し、その熱で焼結させる方式です。
金属のほかにナイロンや樹脂も用いられるケースがあります。
従来は金属を3Dプリンターで造形する際の主要な方式でした。
ナイロン樹脂やエラストマーのほか、金属やセラミックによる造形も可能です。
メタルデポジッション方式
粉末床溶融結合方式は敷き詰めた粉末床(パウダーベッド)に対してレーザーを照射するのに対し、メタルデポジッション方式は粉末の噴射とレーザーの照射を同時に行いながら造形していく方式です。
金属の3D造形としては造形スピードが早く、金属粉末を除去する作業が不要というメリットがあります。
まとめ
今回は3Dプリンタについて知りたい方、これから3Dプリンタの導入を考えている方向けに
本記事では
・3Dプリンタとは?
・3Dプリンタの特徴
・3Dプリンタの造形方式の種類と特徴
などを解説しました。
今回はいくつかの代表的な造形方式を紹介しましたが、これらはいずれもコストや造形時間、使用できる材料、得意とする用途などが異なります。
3Dプリンターによる造形をより効率よく活用するためには、適した用途によって使い分けることが必要です。
高い精度が求められる造形や、自社で所有する3Dプリンタでは対応できないような大きなサイズの製作は、ノウハウと経験を持つ業者へ依頼することをおすすめします。
本記事が3Dプリンタについて知りたい方、これから3Dプリンタの導入を考えている方の参考になれば幸いです。
最後までご覧いただき、ありがとうございました。